In today’s maritime industry, there is an increasing demand for innovative and eco-friendly solutions. These should not only meet the current environmental requirements but also be able to operate in demanding conditions, while keeping OPEX to a minimum.
The HST Ella is such a vessel. A hybrid CTV designed to provide crew and equipment to wind farm installations in the UK North Sea, as well as French offshore wind farms.
In this case-study we will look at how a tailored hybrid power- and propulsion-system is implemented successfully, and how efficiency and sustainability does not get in the way of power and operational profile requirements.
What is a CTV
A Crew Transfer Vehicle (CTV), as the name implies, is a ship used to transfer industry crew and equipment to offshore installations. In a growing extent they are aimed at wind farms offshore. They are designed for an operational profile of high-speed journeys, approx. 30 knots, with journeys of 40-120 minutes duration, back and forth to wind farm installations. Disembarkation often happens at the bow, so the vessel must also be capable of a high Bollard push, securing the boat in potentially rough waters, in addition to high-speed transit operation.
They see a lot of varied work, so efficiency and reducing the interval of maintenance/overhaul is an important aspect of their design, minimizing OPEX.
Maneuverability and robustness are also important. The craft must be able to berth to a variety of rigs and installations, providing a range of other duties alongside personnel transport. The demanding waters offshore, can make environmental and emission considerations a challenge, as such vehicles often require more power. However, a cutting edge hull design, unique propeller tunnel, and a tailored hybrid power and propulsion solutions are an elegant way of solving it.
“HST Ella” Objective & Aim
The HST Ella was designed specifically for the sea-based wind farm sector. Its maiden contract was at East Anglia ONE offshore wind farm, which lies 43 km (27mi) off the Suffolk coast, in the UK North Sea. In this demanding environment, it meets future regulations on emissions while retaining a strong operational profile and reducing the operators OPEX.
This hybrid CTV is capable of 10 knots on electric and 30 knots on diesel power. It is designed to carry 24 people, together with 15 metric tons of payload, providing a wide range of supporting roles.
Tailored solution
Servogear was approached by the ships designer Chartwell Marine, to provide the vessel’s propulsion and power system. Based on the HST Ella’s hull design, Servogear tailored a custom hybrid system, optimized for its hull, weight, and hydrodynamics.
Two Servogear HD295 PTI gearboxes allow the electric propulsion motors, normally used at slower speeds close to port, to act as generators during the high-speed diesel-powered transit between shore and installations. This charges its batteries, which provide both the propulsion- and onboard (hotel)-power.
A spur-gear has also been delivered together with the electric motor to enable a lower propeller RPM during electric operation. This increases the propulsion efficiency considerably, since one can run at a much higher propeller pitch.
Coupled with dual 1200 mm Servogear Ecoflow Propulsor controllable pitch propellers (CPP), you have a recipe for success. A carefully considered system, where Servogear had to balance every component towards the goal of a lightweight, robust, high-speed, and low-emission vehicle.
Propeller, its axle and tunnel, rudder, brackets, reduction gears, diesel - and electric engines with spur-gears, as well as batteries, must come together perfectly to achieve the set goals. By ensuring that each component is operating at maximum efficiency, the propulsion system's energy consumption can be reduced.
A completely custom solution is the only way to achieve such results, and Servogear have decades of experience in optimizing it. Some specialized components, like propeller blades, are installed by Servogear personnel at the Diverse Marine shipyard, but otherwise the system is constructed and installed by the ship builder itself, based on Servogear's specifications.
Achievements
Such a custom hybrid solution requires a larger investment, about 30%, but makes up for it with its reduced fuel- and energy-consumption. Before a permanent charging solution was established, charging was done at the open sea by the diesel engines. Despite this, the fuel-consumption went down over 20%. Once on-land charging was constructed, this rose to over 25% reduction, compared to similar vessels.
Additionally, not having the diesel engines running constantly, reduces their running hours, which in turn significantly extends the vessels up-time before required engine overhaul.
The HST Ella is providing a much-improved work environment for its crew and passengers, almost eliminating vibration and noise for much of its operation and compliments the green energy sector it is supporting. Put simply, it’s answering future regulatory requirements and environmental needs today.
Exceeding every expectation
The ship’s operator, High Speed Transfers Marine, have reported exemplary performance in the two years HST Ella has been in operation; it has exceeded every expectation in terms of service requirements, operational cost, and comfort.
Its sister ship, the HST Frances, are showing the same performance and a third vessel of the design is under construction, making this a three for three success story.
Conclusion
There is a way of combining demanding speed and power requirements in a way that faces head-on the strict sustainability goals and regulations of the future. The CTV HST Ella is one such vessel, supporting the growing offshore wind farm industry.
Its hybrid power and propulsion system, tailored by Servogear, are reducing operational costs, both in terms of fuel consumption and maintenance requirements.
The vessel is one out of three sibling ships, where two are already in operation and showing excellent performance. They are not only meeting current and future environmental and regulatory requirements, but be able to operate in demanding environments while keeping OPEX to a minimum.
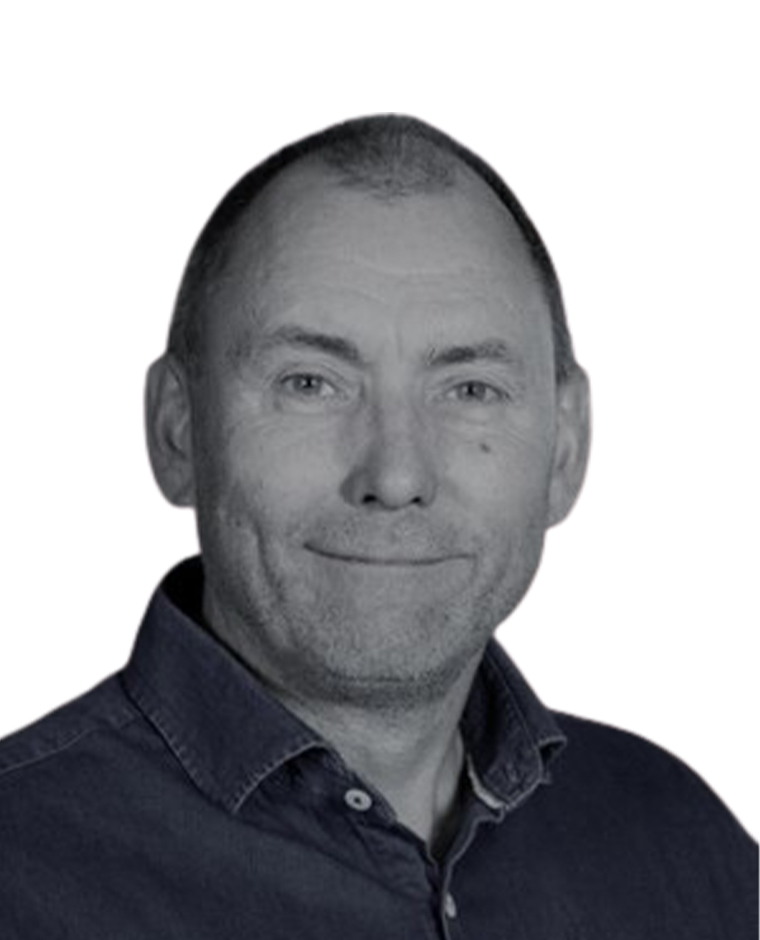